
OFF CAMBER PRODUCTIONS

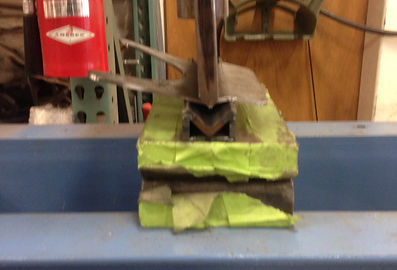
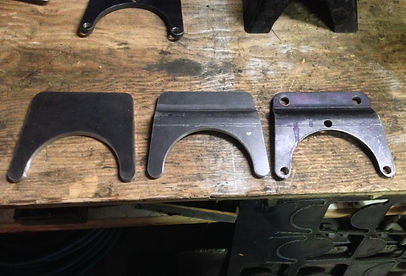
Final Processing:
Once the brackets had been cut and bent to the proper specification, the final step in the build process was drilling the holes in which the bracket would mount to the axle and the holes that held the caliper to the bracket.
Due to the combination Mitsubishi Montero and Ford Mustang Calipers the tolerances of caliper to wheel clearance were very tight. The smallest most common rim to be used on toyota pickups is a 15" wheel. The constraint of using this size rim with the rotor and caliper packed required the holes that were drilled to be within .001" from the location in which they were designed to be. Special care was taken during this step to ensure there would be no interfence.
Bending of the brackets:
The process of cutting out the brackets was the simple part. Once the brackets were cut out two bends needed to be placed in the bracket to ensure the proper offset for the caliper to properly align with the rotor.
The equipment that was available for use was not sufficient enough to bend the thicker material.This reqiured the use of a press brake. Along with a thickness issue the distance between the bends was too close for conventional press brake equipment. This meant building a custom jig specifically designed for bending these brackets.
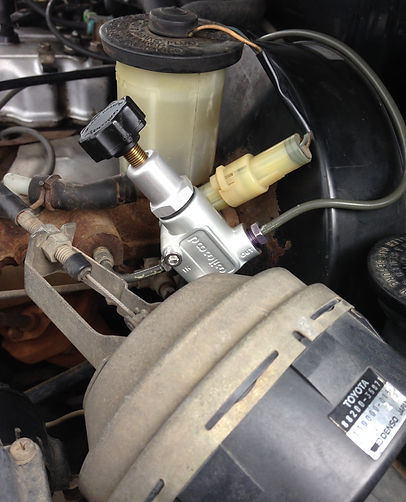
Vehicle Modifications:
The design of braking system the comes stock on the 1986 Toyota pickup is not a common step up. The rear brake system contains a fluid return line and load sensing proportioning valve. The test vehicle's proportioning valve was faulty and leaking causing a dangerous situtation.the proportion valve needed to be removed from the system which in turn required the removal of the return line.
To properly set up the new disk brake conversion a new proportioning valve needed to be implemented which required cutting and reflaring the now only brake line that runs to the rear of the vehicle. Once the new proportioning valve was installed and return line removed, the vehicle was ready for the installation of the new disk brakes.
THE BUILD:
The build process spanned from December of 2014 to April of 2015. This started with the construction of the brackets and covers until the current implementation of the brackets.